多向鍛造概念
多向鍛造是一種封閉式凈成形鍛造加工工藝。它鍛造的產品,不單外形精密,還可擠出產品內孔。所以,用這種工藝生產的鍛件,既有組織結構細密,外觀形狀復雜精密,還可以節約材料,降低能耗,尤其在加工異形內孔類產品時,其優勢更加明顯。精密鍛件如圖1所示。

圖1 精密鍛件
圖2 鑿巖機缸體
圖1中的精密鍛件兩端均為異形內孔。采用多向鍛造工藝生產該產品時,在多向鍛造設備上實現產品內外一火成形,生產效率較原來的常規鍛造工藝提高數倍。多向鍛造工藝的實施有兩大類別:一是在常規鍛造設備上,使用特制多向成形模具實現多向鍛造成形;二是采用多向鍛造專用設備鍛造成形。前者利用常規鍛造設備,配合結構復雜的復合動作模具來實現多向鍛造,其實施噸位非常有限,大多運用于制造小型產品,如五金雜件等。產品單重大都小于一公斤。后者需要專用的多向鍛造設備,前期投入較大,但是工藝性能優越,生產模具相對簡單,適應產品能力極高,一般產品單重10公斤左右,大型設備甚至可以鍛造上百公斤單重的鍛件。所述多向鍛造屬后一類別。我公司有兩條以2000噸級的自制液動多向鍛造機為主機的多向鍛造生產線,先后鍛造加工過鑿巖機缸體、機頭、汽車轉向機、萬向聯軸節、閥體、轉桿接頭等多種類鍛件。
多向鍛造產品工藝
鑿巖機缸體產品形狀如圖2所示。這個產品既有復雜的外形鍛造成形要求,又需要高強度的薄壁缸筒,是一種非常典型的多向鍛造產品,常見的多向鍛造規范中多有提及,下套筒模具結構
如圖3所示,也就是鑿巖機缸體。
在我們采用多向鍛造工藝生產該產品之前,業內均使用常規鍛造工藝如3噸模鍛錘等加工制作。常規鍛造工藝加工的缸體鍛件,其外觀尚能滿足產品設計的質量要求。但是,常規工藝卻只能鍛造出實心體鍛件。在配件的后續加工中,首先要耗費大量的工時來掏空內腔,既耗費材料,又耗費工時,生產效率很低。我們采用多向鍛造工藝生產鑿巖機缸體,不僅外觀質量高,在實現閉式鍛造無飛邊損耗的同時,因為兩側擠制出了預孔,從而進一步大幅度降低材料消耗,也減少了后期掏孔的工時消耗。多向鍛造工件圖如圖4所示。
圖3 下套筒模具結構
1-上模座 2-上墊板 3-上凹模 4-上壓板 5-沖頭6-下凹模 7-下壓板 8-下墊板 9-下模座
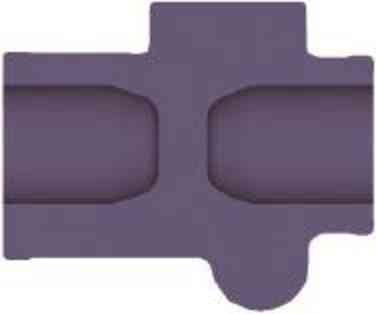
圖4 多向鍛造工件圖
根據我們的實際測算,同規格產品,采用多向鍛造時料耗為12公斤,采用常規工藝鍛造時料耗為18公斤。兩種工藝比較,常規工藝比多向鍛造多消耗材料50%。由此可見,多向鍛造在節能降耗方面具有相當明顯的優勢。
多向鍛造不僅省料,還能巧妙的節能。仍然按前述鑿巖機缸體鍛件為例,常規工藝為3噸模鍛錘鍛打成形,我們用2000噸液動多向鍛造機鍛制。多向鍛造機是由兩個側缸來施加成形能量的,該油缸的設計噸位僅僅300噸。如果按照普通理論知識所述,采用多向鍛造工藝鍛造這個產品時,模具結構圖如圖5所示 。
按照這個模具結構,其端面沖頭截面形狀如圖6所示。由此圖形可得到端面沖頭面積約為130cm2,以產品成形流動應力按600MPa計算,理論成形噸位為780噸。我們在模具設計中,充分利用閉式模具的成形特點,沖頭形狀等同鍛件內孔尺寸,從而有效的降低了產品的成形噸位。改進后模具結構如圖7所示 ,改進后沖頭截面如圖8所示。
圖5 模具結構圖
圖6 端面沖頭截面形狀
圖7 改進后模具結構
圖8 改進后沖頭截面
圖8中陰影內圓是改進的沖頭截面,面積只有約35cm2,按照同樣的成形流動應力計算,所需成形噸位僅為210噸。除了中空類鍛件,對于一些外形復雜的鍛件,多向鍛造也具有工藝簡單、生產效率高、產品質量穩定的長處。多向鍛造轉向節鍛件如圖9所示。
用傳統工藝鍛制該產品,需要通過比較復雜的制坯,初鍛工步之后才能進行終鍛。其生產過程占用設備多,使用生產人員多,生產周期長。而采用多向鍛造制造同一產品,無需任何預加工工步,材料加熱后直接裝模成形,工序鏈短,操作人員少,生產周期短,正所謂實實在在的多快好省。多向鍛造實物照片如圖10所示。
由產品圖片可見,鍛件符合凈成形的精鍛要求,少無飛邊,除了具備前述工藝優點,相比常規工藝鍛造還可以節約10%~15%的飛邊料耗。
圖9 多向鍛造轉向節鍛件
圖10 多向鍛造實物照片
結束語
近年來,國內的多向鍛造生產已經在諸多行業崛起,尤其在國家重點項目當中已經做出了卓越的成績。不過,多向鍛造工藝還有許多應用領域尚待開發。相信在不遠的將來,多向鍛造必然會發揮出更加卓越的實際效益。